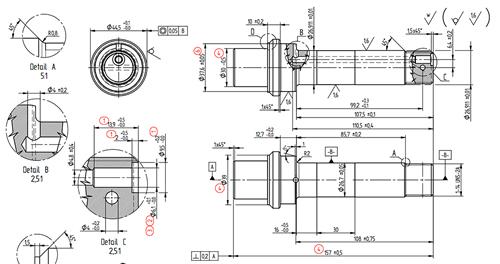
At that time, the client didn't provide us drawings, technical requirements and samples, but only a rough drawing with basic dimensions, and it is also not clear about which material to use. Under this case, we gave some suggestions to the client, and he purchased several samples from local after market, delivered them to us and said that the demands for the sample products in the local market were sizable, with a monthly consumption of over 100,000 pieces. We therefore conducted physical and chemical tests on the samples and made out chemical elements and contents in the samples and then confirmed the specific materials and presented the customer with a drawing and 3D model.
The client confirmed the drawing and technical requirements very soon and we also provide a reasonable price on the product. Finally the client asked us to deliver him with 10 pieces of samples within 20 days, and everything went well.
We received "unqualified" feedback form the client after 6 days of samples delivery. The reason was that the mechanical performance didn't meet the requirements. We thought that it might be the problem with the raw materials, then we had a mechanical property test on the left samples and found that both the tensile strength and yield strength didn't meet with the requirements. After several day of discussion and analysis, we finally confirmed that there was decarburization caused by the long time heating of the raw materials in the induction furnace.
The second time we delivered the samples to the client, we got the information that sizes of some products were unqualified, but requires no samples delivery again, and we only need to perfect them in the trial order production. Now the trailer forged components for this client were put into mass production.
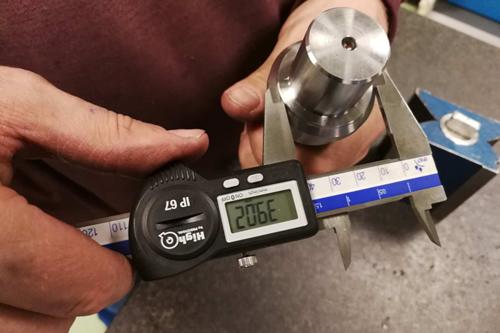
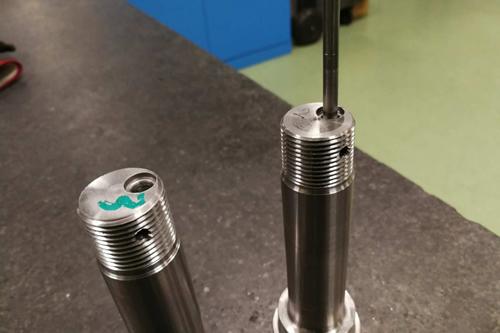
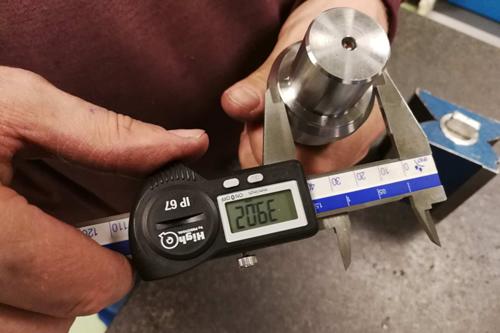
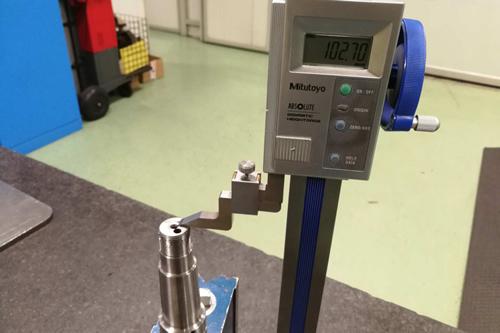
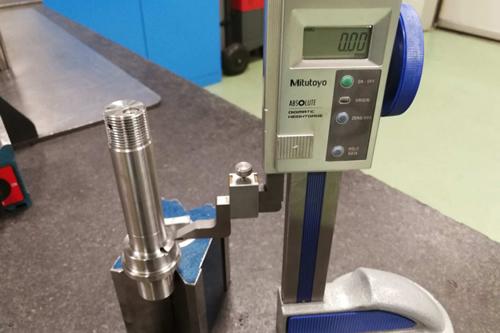